According to the Wooden Boat School, ” Cold molded hulls have been built since the technique was used for World War II planes—often using casein or urea-based glues. Today, one would use epoxy almost exclusively, benefiting from its superior bonding, gap-filling, strength and water resistance.
Advantages are: If well executed, this system produces a very tough, long-lasting hull that is stiff and resistant to damage and rot. It requires only the minimum of internal stiffening. Still a useful option where labor costs are low or just not counted.
Disadvantages: The system is pretty labor intensive and solid veneers of moisture-resistant wood are also becoming expensive and difficult to obtain in some parts of the world. The system also requires a good, solid mold prior to construction, which has no further use after the hull is lifted off. “
The process involves first making a mold (shown below) from ribs and stringers.
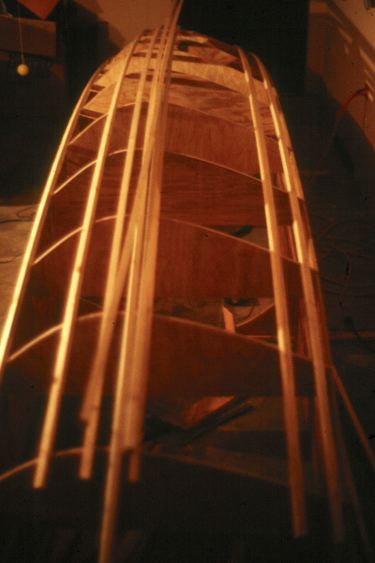
Wood veneers (1/8″ thick Douglass fir in my case) are stapled, at an angle, to the mold. Two additional veneer layers are laid down using two part marine epoxy and staples. NEXT